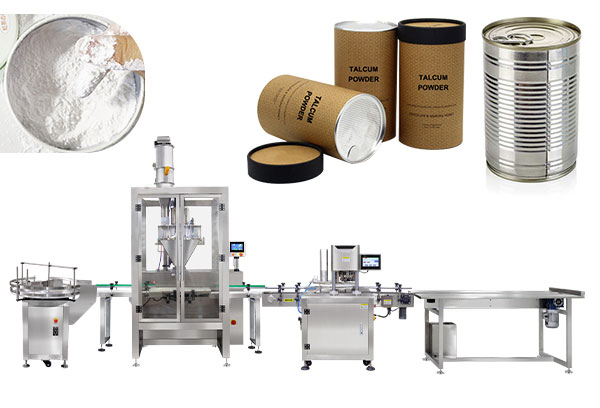
Automatic Talcum Powder Filling Machine For Cans And Tins
Read More
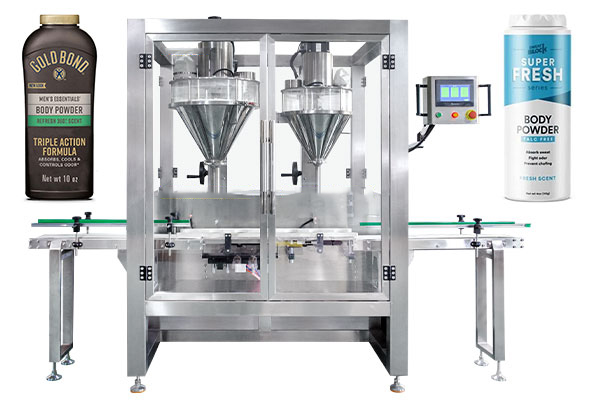
Automatic Talcum Powder Weighing And Filling Machine
Read More
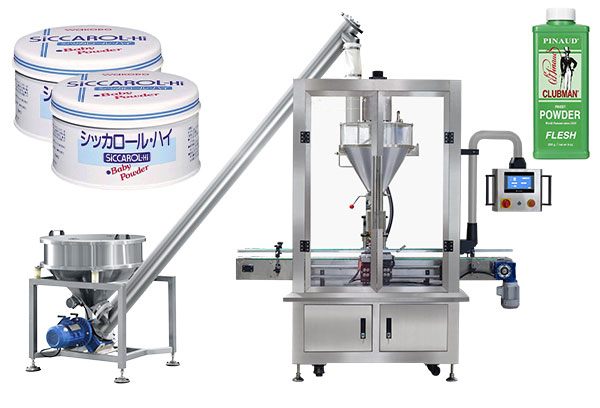
Fully Automatic Talcum Powder Filling Machine
Read More
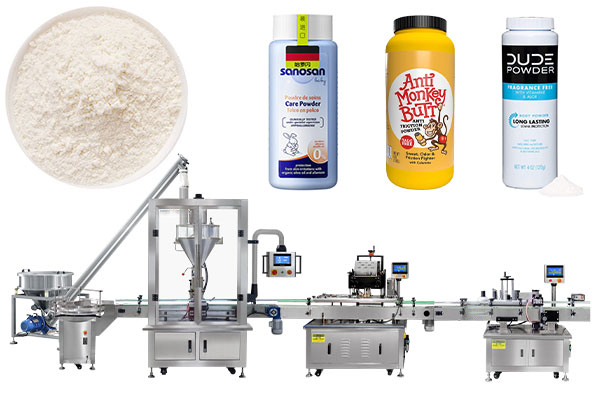
Automatic Talcum Powder Filling Machine With Capping Labeling Line
Read More
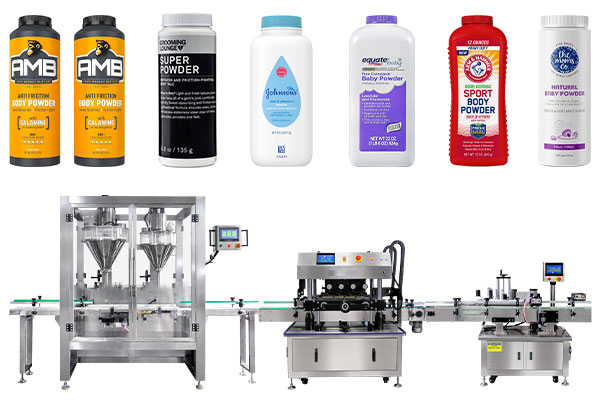
Automatic Talcum Powder Filling Machine With Capping And Labeling Line
Read More
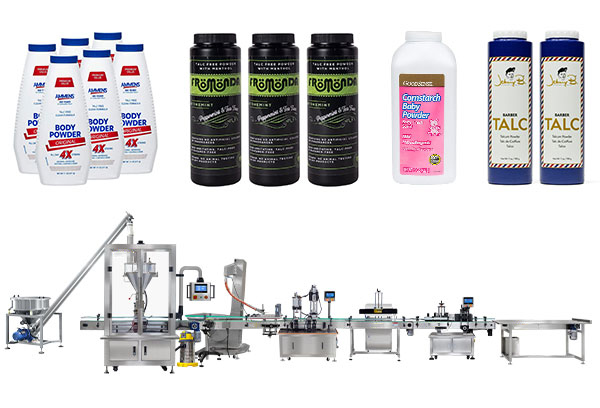
Automatic Talcum Powder Filling Machine With Capping And Labeling
Read More
In the realm of manufacturing, precision and efficiency are paramount. Every step in the production process must be optimized to ensure seamless operations and consistent quality. When it comes to packaging powdery substances like talcum powder, the utilization of specialized machinery becomes indispensable. Enter the talcum powder filling machine – a marvel of engineering designed to streamline the filling process while maintaining accuracy and hygiene standards.
At first glance, the inner workings of a talcum powder filling machine may seem complex, but a closer inspection unveils a well-orchestrated symphony of components working in harmony. Let’s delve into the intricacies of this remarkable apparatus and shed light on its operational mechanism.
1. Powder Feeding System:
The process commences with the powder feeding system, where talcum powder is fed into the machine. This system ensures a continuous and uniform flow of powder, preventing clogs and inconsistencies in the filling process.
2. Filling Mechanism:
Central to the functionality of the talcum powder filling machine is its filling mechanism. Typically, this involves the use of augers or pistons, depending on the specific design of the machine. Auger-based systems employ a rotating helical screw to dispense precise amounts of powder into containers, while piston-based systems utilize the displacement principle to achieve accurate filling volumes.
3. Control Systems:
Modern talcum powder filling machines are equipped with advanced control systems that regulate various parameters such as filling speed, volume, and accuracy. These systems employ sensors and feedback mechanisms to ensure optimal performance and minimize wastage.
4. Container Handling:
Efficient handling of containers is crucial to the overall efficiency of the filling process. Talcum powder filling machines are equipped with mechanisms for container positioning, stabilization, and sealing, ensuring seamless integration with downstream packaging operations.
5. Cleanliness and Hygiene:
In industries where hygiene is paramount, such as pharmaceuticals and cosmetics, talcum powder filling machines are designed to meet stringent cleanliness standards. These machines feature sanitary construction materials and incorporate features such as dust extraction systems to maintain a sterile production environment.
6. Customization Options:
To accommodate diverse production requirements, talcum powder filling machines often offer customization options such as adjustable filling speeds, container sizes, and filling volumes. This versatility ensures adaptability to varying production demands without compromising efficiency or accuracy.
7. Maintenance and Serviceability:
Like any mechanical equipment, talcum powder filling machines require periodic maintenance to ensure optimal performance and longevity. Manufacturers typically provide comprehensive service packages, including routine inspections, spare parts availability, and technical support, to minimize downtime and maximize uptime.
In conclusion, the operation of a talcum powder filling machine is a finely tuned process that blends precision engineering with advanced technology. From powder feeding to container handling, every aspect is meticulously designed to deliver consistent results while adhering to strict quality and hygiene standards. As industries continue to evolve, the demand for efficient and reliable packaging solutions will only grow, making talcum powder filling machines indispensable assets in modern manufacturing facilities.
To explore how our talcum powder filling machines can optimize your production processes and elevate your packaging operations to new heights, contact us today for a consultation.